SEPLITE® LXA88
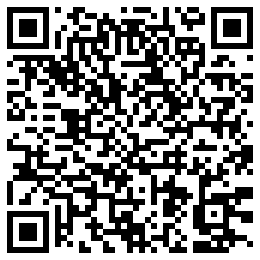
SEPLITE® LXA88 is a macroporous adsorbent with a special matrix structure. The resin has excellent adsorption capacity for tea polyphenols (up to 100mg/g) when it is used in tea extraction. Besides, it hardly adsorbs caffeine. What's more it could also completely separate fat catechins from non fat catechins.
SEPLITE® LXA88 Macroporous Adsorbent Application:
It is mainly used for in the extraction of tea polyphenols.
SEPLITE® LXA88 Macroporous Adsorbent Physical and Chemical Characteristics:
Physical Appearance | Ivory to light yellow spheres |
Particle size (mm) | 0.315-1.25 |
Moisture Content (%) | 70-80 |
Bulk Density (g/ml) | 0.65-0.75 |
Density (g/ml) | 1.15-1.25 |
SEPLITE® LXA88 Macroporous Adsorbent Usage:
1. Resin loading(wet method)
A. Laboratory
Measure: mix a certain amount of resin with deionized water in a beaker, then pour the mixed solution into the measuring cylinder, make sure the resin fully settled. By supplementing and removing, makes the resin bed lies in the same level with the corresponding scale.
Loading: Close the outlet valve at the lower end of the ion exchange column, use water to lead the resin enter the ion exchange column, then open the outlet valve of the exchange column, allow the resin to settle and compact in the column. At last, close the outlet valve(Note: The liquid level must be kept 1~2cm above the resin bed, avoiding dry columns.).
B. Industrialization
Before resin filling, clean the resin adsorption column and relevant pipes with clean water and alkali solution, and clean the welding slag and the sediment dust attached to the pipe wall. After that, inject 1/3 of the volume of water into the resin column, then start filling the resin, check the drain cap, Intercepting at the drainage outlet with mesh screen(>=80 mesh), check whether there is resin leakage. It is normal when there comes out a few tiny spheres. While if there has some macro resins comes out, it may identify there may be some problems of the filter plate. In this situation, drain the resins and water, check out the filter plate and repair it. Then repeat the test according to the method above until it meet the requirements. After that, add the remained resins into the column.
After the resin is filled, reverse the resin with deionized water at the flow rate of 2~4BV/h for 1 hour, then let the resin settled completely. At last clean the resin bed with deionized water at the flow rate of 2~4BV/h for 1 hour.
2. Resin pre-treatment
First, Carry out the column treatment with 4% sodium hydroxide solution, the flow rate was controlled at 1~2BV/h, and the treatment volume was 3~4BV; after the treatment was completed, use the deionized water to clean the alkali in the column bed and the resin channel, until the pH of the outlet liquid is lower than 10, stop washing,. Make sure there would be at least 20~30cm of liquid surface layer kept on the resin bed to prevent column drying; Then use 4% hydrochloric acid solution to carry out the column treatment, the flow rate should be controlled at 1~2BV/h, and the treatment volume is 3~4BV; after the treatment is completed, the residual acid in the column bed and the resin channel should be washed off with deionized water. When the pH of the outlet solution is higher than 4, stop the water washing. Make sure there would be at least 20~30cm of liquid surface layer kept on the resin bed to prevent the column drying.
Soak the resin in the column with more than 95% ethanol solution for 2~4h, and then use the same ethanol solution for the column treatment, the treatment flow rate should be controlled at 1~2BV/h, the processing volume is 2~4BV. When the dilution is not turbid, stop the washing. Finally, wash with deionized water until the ethanol content at the outlet is less than 1% or there is no obvious ethanol odor. Make sure there would be at least 20~30cm of liquid surface reserved on the resin bed.
3. Resin adsorption
Before the adsorbing, it must be carried out necessary pre-treatment to remove the solid impurities to prevent the resin pores being blocked. The adsorption process generally adopts the way of passing through the column in the forward direction. The adsorption flow rate is generally recommended to be controlled at 1~3BV/h. The content of the target substance in the outlet liquid should be detected to check out the adsorption status of the resin.
4. Water washing
After the resin adsorption is completed, the resin column bed should be cleaned with deionized water for 1-2 hours at the flow rate is generally controlled at 1~2BV/h to remove the residual liquid and some water-soluble impurities.
5. Resin desorption
Firstly use low-concentration ethanol (less than 25%) to wash the impurities, then use high-concentration ethanol (more than 75%) to desorb the tea polyphenols. The specific process could also be adjusted according to different raw materials and requirements.
6. Resin regeneration
After the resin was used for a period of time, when the adsorption capacity shows a decline, you may try a deep regeneration treatment for the resin, the treatment method is listed as follows:
1)Alkali Regeneration:
Heat the 4% sodium hydroxide solution to 80~85℃, passing through the column in the forward direction, carry out the regeneration treatment for the resin by alkali. The flow rate was controlled at 1~2BV/h and the treatment was about 1.5 hours. After the hot alkali regeneration treatment is completed, use deionized water to clean in the forward direction, and the cleaning
flow rate is 2~3BV/h until the pH of the liquid is no more than 10.
2)Acid Regeneration:
After the alkali regeneration, use 4% hydrochloric acid solution to carry out column treatment in forward direction, the flow rate should be controlled at 1~2BV/h, and the treatment is about 1.5hours. After the acid regeneration treatment is completed, use the deionized water to clean, and the flow rate should be 2~3BV/h until the pH of the liquid is not less than 5.
3)Attention:
a. Avoid loading and unloading of the resin repeatedly to prevent uneven flow of the resin bed which may cause bias flow
b. If it is out of operation for a short period of time, the resin should be regenerated, cleaned and soaked in clean water.
c. If it is out of operation for a long time or the room temperature is lower than 5â?in winter, the resin should be soaked in 15% NaCL or 10% sodium hydroxide aqueous solution, this will prevent the resin from freezing and the growth of bacteria.
d. The liquid must carry out necessary filtration treatment before being put on the column to remove solid impurities, it could also prevent the blocking of the resin pores, which will affect the resin adsorption effect.
Precautions:
Resins should be stored in sealed containers or bags where temperature was above 0℃ in dry conditions without exposure to direct sunlight. Do not mix ion exchange resin with strong oxidizing agents; otherwise it will cause violent reactions.
In case of eyes contact with resins, rinse eyes immediately with plenty of water, and consult a specialist. Material and samples must be disposed according to local regulations.
Dry polymers will expand when become wetted and may cause an exothermic reaction. Spilled materials may be slippery.
SEPLITE® and Monojetâ?are registered trademarks of Sunresin New Materials Co. Ltd., Xi`an
This information is general information and may differ from that based on actual conditions. For more information about SEPLITE® resins, please contact SUNRESIN® directly.
All information set forth herein is for informational purposes only. This information is general descriptive(introductory) information of SUNRESIN and its related products, technologies and services. Neither shall constitute the guarantee of SUNRESIN and its affiliates to products, technologies and services in specific fields and specific application conditions results, unless otherwise expressly noted. SUNRESIN and its affiliates assumes no obligation or liability for the information in this document. Customer is responsible for judging whether the information is appropriate for Customer's concrete demand and are obliged to understand whether the use of these products, technologies and services is permitted by the laws and regulations of their countries and relevant regions. Unless expressly stated, no freedom from infringement of use any patent or trademark or intellectual property rights owned by SUNRESIN or its affiliated companies under this document is to be inferred.